Humans have been gliding on snow for ten thousand years. As long as there have been humans strapping skis to their feet, there have been other humans ensuring that those skis are well-maintained and tuned to the task at hand. Whether trekking across miles of snow and ice to hunt a walrus or grabbing your lunch lap to engender envy among your work-bound peers, it is more effective (and fun) when your skis work.
The material that makes up the base of modern skis is called Ultra High Molecular Weight Polyethylene. No catchy nicknames, just good old UHMWPE, as apparently the lab marketing department was off on holiday at the time of its creation. Prior to the invention of UHMWPE in 1962, ski bases were nearly universally made of some variety of wood, which required an entirely different approach than taken by today’s ski tuners.
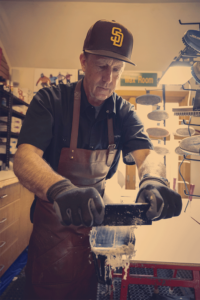
Ketchum’s Wax Room owner Curtis Bacca practices the art of ski tuning, demonstrating the process of a proper tune. As a master of the art form, Bacca emphasizes the quality of a hand-tuned ski.
Tuners of yore spent most of their time ensuring the wood grains of the ski were fully impregnated with either pine tar or a natural oil like linseed. A deft hand would apply heat with a torch to open up the wood’s pores, ensuring the tar or oil seeped to the depths of the grain. The goal of this process was to make certain that no moisture from the snow would find its way in to wreak havoc on the shape and sturdiness of the ski. After this process, the final preparation was the familiar addition of wax to the bases.
For modern skis, the process looks very different, and it is the UHMWPE that gets a good portion of the attention. Though the material is impervious to moisture, its perfectly smooth finish requires grinding to give it the structure required to retain wax and decrease friction. Then there are the metal edges, which require beveling, sharpening and polishing, an awful lot for a ski tuner to work with when dialing in a ski to its rider.
Though it took 9,900 years to make a change from wood, the last hundred years of ski technology have seen swift and steady advancements, including the tuning trade tools. Founded in 1952, German machine company Wintersteiger quickly became the premier name in ski tuning tech, and its supremacy remains relatively unchecked today. Their latest machine released in 2021, aptly named Jupiter, is a monstrous all-in-one, fully automated ski servicing machine that grinds, bevels, sharpens, and waxes.
With such advanced automated technology, who needs a good old-fashioned hand-tuned ski? According to Curtis Bacca, owner of the Wax Room in Ketchum and legendary ski tuner who has spent the last 30 years tuning planks across the globe for Olympians and world champions, absolutely everyone.
“Everyone skis differently,” says Bacca. From a skier’s size and weight to their skill level and style, even down to the temperature and crystal shape of the snow on a given day (really), everything factors into the tune you should be applying to your skis.
Bacca acknowledges that there is definitely a place for the Wintersteiger Jupiter in the ski industry, like high-volume rental shops. But he’s also quick to point out that a truly custom tune will make anyone ski better and just plain have more fun. “If you haven’t had [a custom tune] to that level, you just don’t know what you don’t know,” he says.
A truly custom hand-tuned ski might be harder to find these days with the steady leaps in technology, but as long as dedicated craftsmen like Bacca and devoted DIYers are in shops and garages melting wax as the snow piles up, your next best day on the hill is probably just one tune away.